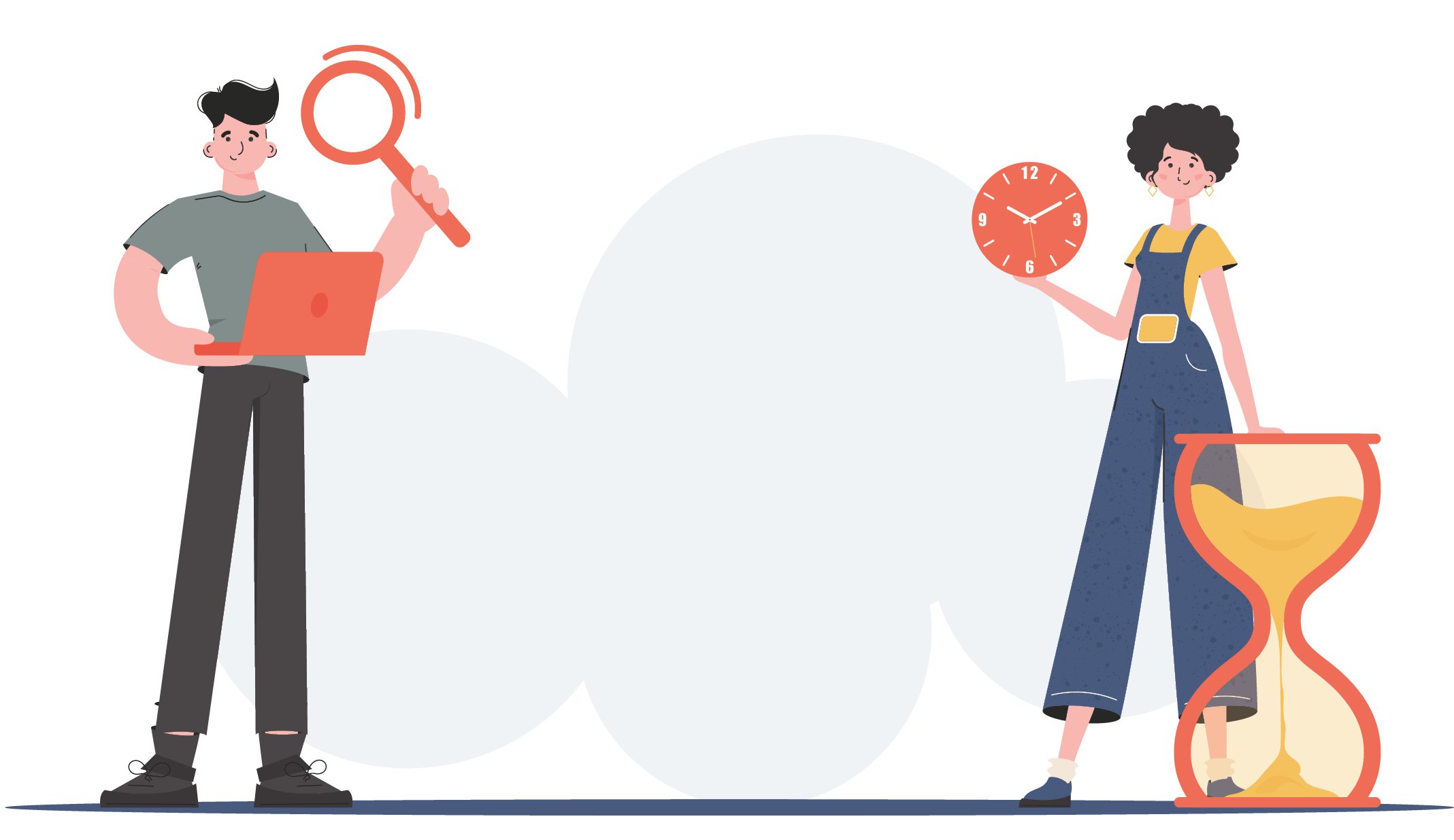
Electric vehicles (EVs) provide environmental benefits, enhanced technology and lower fuel costs. But repair shops and fleet operators are facing a pivotal moment as EVs become increasingly prevalent.
Although some repair shops have successfully transitioned, many continue to struggle with effectively servicing EVs due to their unique requirements.
Unlike traditional internal combustion engine vehicles, EVs are equipped with intricate electronic systems, high-voltage components and specialized battery technology. Addressing these challenges requires highly skilled technicians well-versed in EV diagnostics, repair procedures and safety protocols, alongside a developing supply network aimed at minimizing maintenance and repair delays.
Let’s review the various factors contributing to EV repair delays and the challenges faced by technicians, facility operators, manufacturers, and consumers.
Limited service infrastructure
Compared to traditional auto repair facilities, the infrastructure for servicing EVs is still evolving. Many repair shops may lack the specialized equipment, charging stations, proper location or certified technicians to effectively manage EV diagnostics and repairs. This can lead to longer wait times as owners travel to authorized service centers or wait for mobile technicians to become available, especially in areas with limited EV adoption.
EV repairs involve stringent safety protocols due to the high-voltage systems present in these vehicles. Technicians and repair facilities must adhere to strict safety guidelines to prevent accidents or damage to the vehicle and personnel.
Technicians require specialized training to diagnose and troubleshoot issues unique to electric vehicles. This includes handling electric components and following manufacturer-recommended procedures. Furthermore, technicians need an understanding of high-voltage systems, battery management, regenerative braking, electric motor operation, heating and cooling systems as well as using insulated tools and personal protective equipment.
Enhanced diagnostic skills can expedite the identification of problems, leading to faster repair turnaround, increased local billable hours and often lower cost as well as inconvenience to the customer.
Unlike traditional internal combustion engine vehicles, EVs rely on specialized batteries, electric motors and electronic systems, which may not be readily available in local markets.
Supply chain challenges
One of the primary reasons for EV repair delays is the intricate supply chain involved in sourcing parts and components.
Unlike traditional internal combustion engine vehicles, EVs rely on specialized batteries, electric motors and electronic systems, which may not be readily available in local markets. This can lead to extended wait times as repair shops and manufacturers struggle to procure the necessary parts, especially for less common models or older EVs.
As we know, this is not isolated to EV and hybrid vehicles as many new vehicles have experienced computer chip and other component delays leading to new vehicle delivery periods that can be as much as 24 months. The pandemic can’t only be blamed for these issues: I purchased a new 2019 Ram 1500 — although an excellent vehicle, I waited almost four months for a windshield and over six months for a replacement stereo system which is integrated with the navigation system, requiring the entire unit be replaced. This leads to our next factor.
Technical complexity
The advanced technology powering EVs presents a double-edged sword. While it offers superior performance and efficiency, it also increases the complexity of repairs.
Unlike conventional vehicles with familiar mechanical systems, EVs incorporate intricate electronic systems, software integration, and high-voltage components. This complexity can lead to increased potential for breakdown and increased time to repair. It also requires highly skilled technicians with specialized training and tools, leading to a shortage of qualified personnel capable of addressing EV-specific issues promptly.
As of writing, I have two EVs currently at the dealership or waiting for parts. My Kia Soul EV has had a high-voltage battery replaced under warranty but has been waiting off and on for almost six months for parts to complete the repair. My other EV, a Volvo XC90 T8, is currently at the dealership for repair of the electrical system and they have reached out to their technical support team.
Dealers or manufacturers often have the benefit of reaching out to their technical teams either in Canada or abroad to support diagnostic issues, like what we have seen with computer systems and advanced electronics. Unfortunately, independent repair facilities or fleet operators that have not prepared for EVs in their shop may not have this level of support, often needing to rely on the local dealership or manufacturer leading to delays, fewer billable hours and customer frustration.
As of writing, I have two EVs currently at the dealership or waiting for parts.
Manufacturer support and parts availability
The level of support and parts availability from EV manufacturers varies widely, impacting repair timelines significantly.
Manufacturers may have robust support networks with readily available parts and technical assistance, leading to faster repairs and minimized downtime. However, others may struggle to meet demand, especially for older models or discontinued components, resulting in extended wait times and frustration for owners and repair shops alike.
Like computer systems, the advancements in EV electrical and battery systems coupled with limited production have led to some parts not being available.
Software and firmware updates
Although not new in today’s world of computer monitoring and control, EVs rely heavily on software and firmware to control various systems, including battery management, regenerative braking and drive modes.
While over-the-air updates have simplified software maintenance to some extent, they can also introduce new issues or compatibility issues with older hardware. Technicians must stay updated with the latest software protocols and diagnostic tools, adding another layer of complexity to repair processes and potential delays.
Batteryspecific concerns
The battery pack is a critical component of any electric vehicle, and its repair or replacement can significantly impact repair timelines. Battery issues such as degradation, cell imbalance or thermal management problems require careful diagnosis and often involve specialized procedures.
Moreover, the cost of replacing a damaged or worn-out battery pack can be prohibitively expensive, leading to longer repair times as owners explore alternative solutions or seek warranty coverage.
Insurance and warranty procedures
Insurance coverage and warranty policies for EVs can also influence repair delays and customer experiences.
Delays may occur as repair shops navigate insurance claims, obtain approvals for repairs, or negotiate warranty coverage with manufacturers. My Kia Soul waited several weeks for various approvals under warranty.
Additionally, limited coverage for certain components or aftermarket modifications can complicate repair processes and lead to longer wait times as owners explore alternative options or seek reimbursement for out-of-pocket expenses.
Despite the challenges, the EV industry is actively pursuing innovative solutions to streamline repairs and reduce downtime.
Seeking solutions
Despite the challenges, the EV industry is actively pursuing innovative solutions to streamline repairs and reduce downtime. This includes advancements in predictive maintenance algorithms, remote diagnostics and modular design approaches that simplify component replacements.
Additionally, collaborations between automakers, repair networks, and technology firms aim to standardize repair procedures, improve parts availability and enhance overall service efficiency for EV owners.
By investing in comprehensive training programs that cover these essential areas and prepare for EVs, repair shops can empower their technicians to deliver faster and more efficient electric vehicle repairs. Additionally, ongoing education and certification programs ensure that technicians stay abreast of evolving EV technologies and industry best practices, further enhancing their ability to reduce wait times and improve overall service quality.
In general, repair delays stem from a combination of technical complexity, supply chain challenges, limited training or knowledge and evolving industry dynamics. Addressing these challenges requires collaboration across the automotive ecosystem, including manufacturers, repair facilities, regulators and consumers.
By investing in training, infrastructure, and technological innovation, the industry can overcome these obstacles and deliver a more seamless ownership experience for EV enthusiasts worldwide.
David Mayers is chief executive officer at Environmental Motorworks, an innovative services company centred on providing hands-on EV and hybrid training to technicians and fleet operators in the automotive and heavy equipment sectors.
This article originally appeared in the Spring 2024 issue of EV World
Leave a Reply